One of the most common problems in locking hardware is incorrectly attributing issues to faulty hardware when, although showing symptoms, it could be power-related. In fact, 50% of Command Access support calls relating to hardware problems are actually power supply issues.
Typical power-related issues can be caused by issues such as distance between power supply and hardware, wire gauge size (or mixing gauges), and power quality which all need to be evaluated.
While hardware failures do occur, they make up only one part of the equation. Power supply-related issues can masquerade as hardware problems because it is the hardware that manifests the problem symptoms. This can lead to an incorrect diagnosis, wasting time with returns and service calls and unnecessarily increase the number of site visits. Worse still, some of these issues don’t manifest themselves at installation.
Let’s break down these common issues to help you stay one step ahead and correctly diagnose problems you might encounter.
Linear vs Switching Power Supplies
A switching power supply may test and work, however there may be hidden issues.
A switching power supply operates by rapidly switching the AC input voltage on and off at a high frequency. Switched mode power supplies utilize electronic switches, typically transistors, to regulate the output voltage. The input voltage is converted into a series of pulses, which are then filtered and smoothed to produce a stable output voltage.
Linear power supplies, however, regulate the output voltage by dissipating excess power as heat. They use a linear regulator to adjust the input voltage to the desired output voltage. Linear power supplies have capacitors on board. Large capacitors store power so it's available for electrified hardware, versus switching power supplies that must gather the power. Switching power supplies don’t have capacitors, so while they may be designed for high efficiency , they were really designed for access control systems (CCTVs, cameras, etc.) that don’t have large initial energy requirements.
For example, after a lunch break where there’s a large influx of employees using one door, you may experience reliability issues that restrict access because there isn’t a pool of power readily available. Linear supplies have these pools of power readily available. In instances of failure, the motor will start to retract, but soon run out of energy and releases. This leads to people thinking they have a motor or adjustment failure, but really, it’s not getting the power needed to reach full retraction.
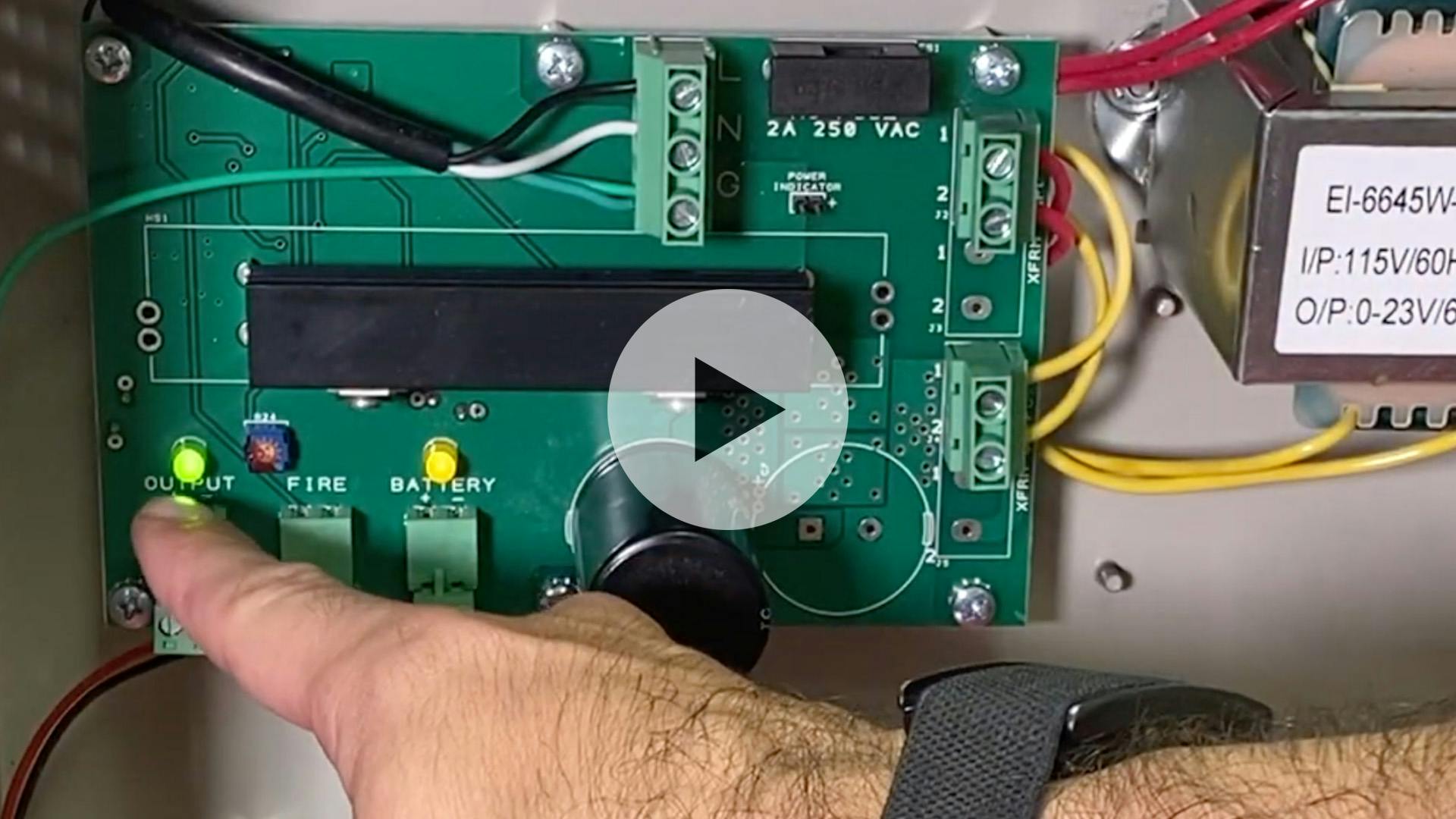
Overview video the Command Access Power Supplies
Distance and Gauge Issues
Another issue people run into is when someone is testing their power supply right at the door, or at the bench with no load on it. This can work upon testing, but when moving it 75 feet away, can lead them into performance problems.
Power supplies should be able to run within 300 ft which at ~24v requires 18g wire to achieve consistent reliability.
The same concept applies when mixing gauges. When working with power transfer hinges, you can use smaller gauges such as 20g depending on what you’re powering up, installers should know that imported hinges often have only 28g wire. For power transfer, Command Access’ standard is 20g, and for those working with hinges day in and day out that difference is noticeable. Many aren’t even aware a 20g is possible on a hinge. This leads to installers trying to put two pairs together, thinking they can “add up” to 18g, but this bundling doesn’t work and can lead to further issues.
Field Testing
Command Access recommends field testers for installers who are working on electrified hardware and want to test the product after installation. It’s handy for troubleshooting when your hardware is not working properly, and you want to identify if it’s a hardware or a power supply issue.
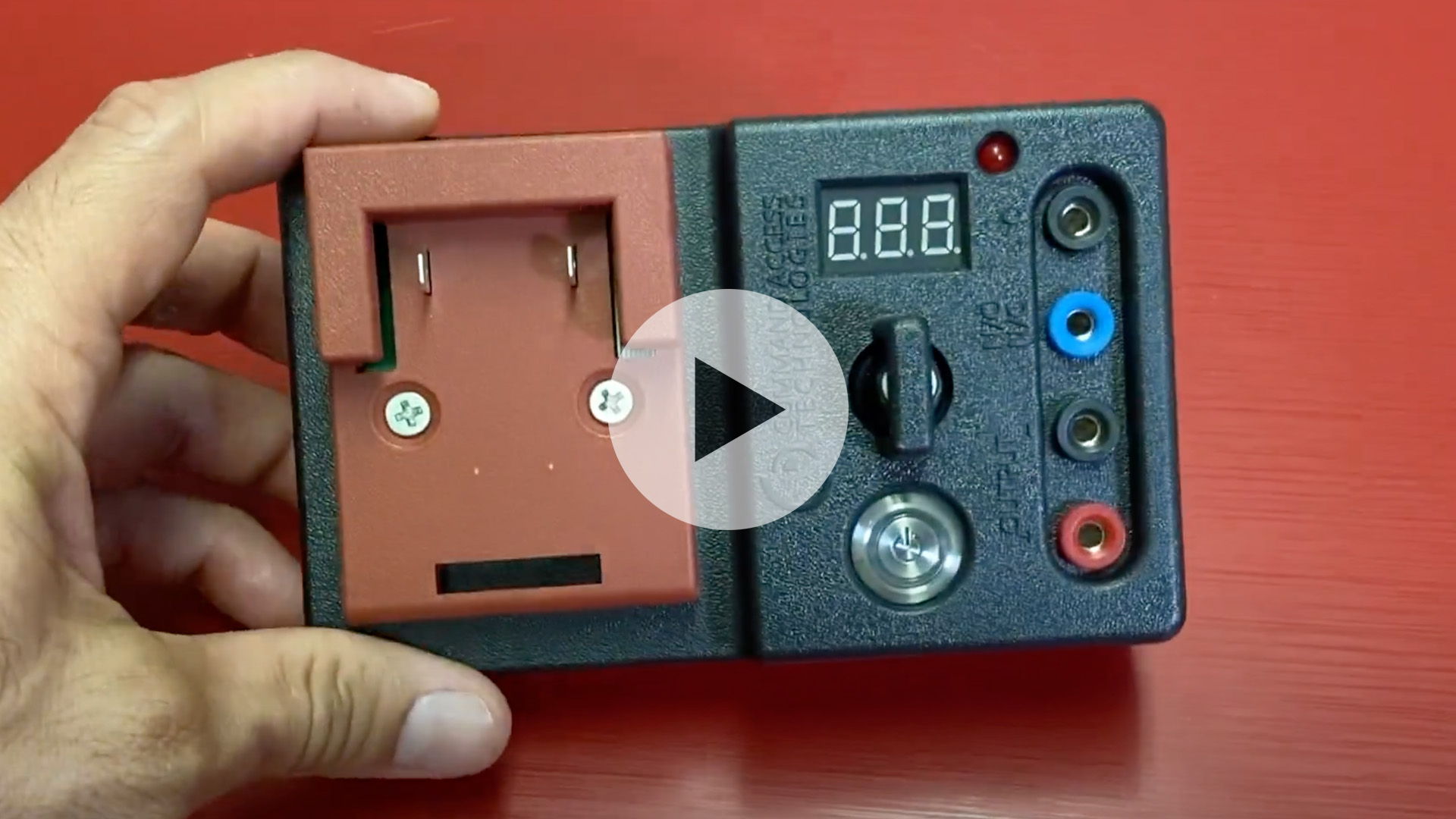
Overview video the Command Access Field Tester
Command Access recently received a tech call from someone experiencing issues with the linear power supply. It was a 4 Amp power supply that would work using 1-3 devices. Once he added a 4th, he had issues with the kit. They were able to use the field tester to confirm the 4th unit worked and confirm it was not an issue with the motor. From that, they were able to pinpoint that an additional 2 Amp boost was needed. Because of this, Command Access recommends you plan to use 80% of available power, even with good power supplies, to avoid this problem. This is why Command Access offers the boost current, to increase the capacity 20% for the inrush.
A field tester is also handy because with power supplies, you have two industries overlapping. Sometimes the door hardware person is the one supplying the power, while other times it's the security integrator. If a door hardware person is subbing for a security integrator, they don’t supply their own power supply. They’ll simply install the hardware and power transfer and will leave loose wires. When the security integrator needs to tie everything together with the access control systems and hook it up to their power supply, they might assume it’s a hardware issue. The field tester can help show there’s no issue at the hinge or exit device.
Products from Unreliable Factories and Vendors
Buying non-branded products can result in various issues too. If you purchase something off Amazon that looks like it matches the specs you need but isn’t coming from a reputable factory, it’s just another potential failure point.
Command has encountered this problem firsthand. They have had vendors change what electronic components are put on a board without notifying them. Because they’re manufacturers who do quality testing, they’re able to catch these issues. If you’re someone just buying off a non-branded product, it might work one day but there’s no guarantee the product will be the same each time you order it.
When you buy from a reputable factory or only authorized vendors that include a warranty, you’ll know that what you’re getting is up to spec. When you buy from one you’re unfamiliar with or who doesn’t back their products with a warranty, it can be a roll of the dice with anything from voltage regulation to a functional bridge rectifier.
Because they’ve dealt with many customers opting for returns and replacements due to these reliability issues, Command Access increases their warranty from 3 to 5 years when you purchase power supplies with their new MLRK1 kits.
Identifying the Problem is the First Step
When your hardware isn’t operating correctly, it can be tricky to nail down exactly what the cause is. Between incorrect gauge size, the wrong power supply design, distance issues, and beyond, it can require some troubleshooting.
Save yourself the time and headaches of returns and service calls by understanding the possibilities, and speaking with an experienced manufacturer that can help you get down to the bottom of it. If you’re interested in learning more about power supplies, field testers, hardware troubleshooting, access management, and best practices, contact Command Access with any questions.